The mantel I originally made for my fireplace was over 22 years old. The style had become dated and with the entire room being renovated so did the mantel. With many different mantel styles out there I had to choose which one. I like how a floating beam mantel looks, so I decided to go with that style.

This was the original mantel I had. As you can see it was quite dated. During our living transformation (another story series) we decided to replace it.
Now comes the next decision. Do I acquire a 6″ x 10″ oak beam approximately 5 feet long or do I create one? I think I’ll go with the creating one since I still have 100s of board feet of red oak. Follow along and see how it turns out.
I start by grabbing several oak boards. I don’t care if they have knots or not because these will only add character to the mantel. After this I quickly just rough mark out the pieces using some chalk to make sure the pieces I want to use don’t fall anywhere that might cause problems.
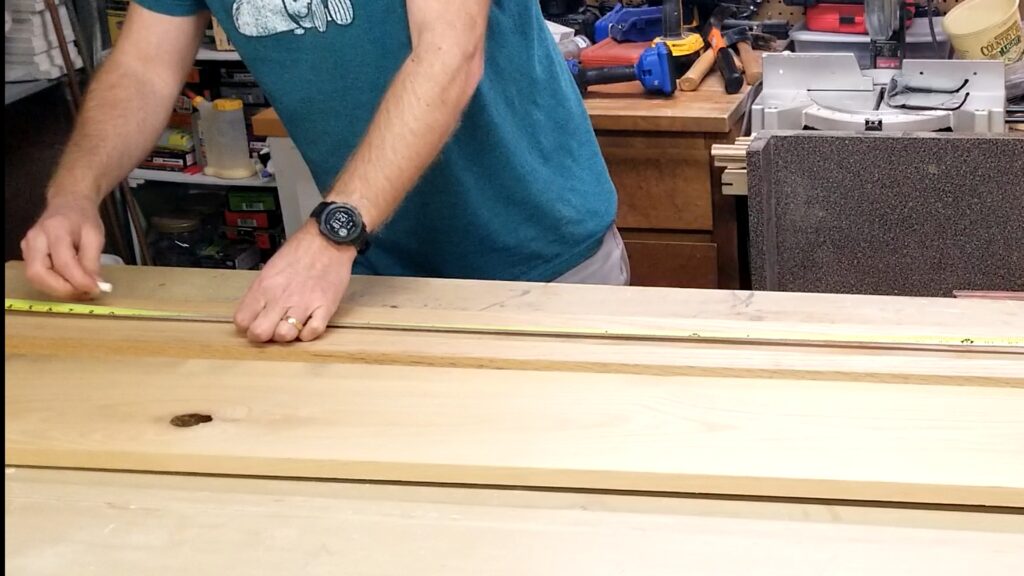
Once laid out, I take the pieces over the miter saw and cut the boards into their corresponding lengths. I then start running the pieces through my table saw to cut them to the proper width. I do this by setting the saw blade at 45 degrees because I will use a mitered joint look to help blend the grain.
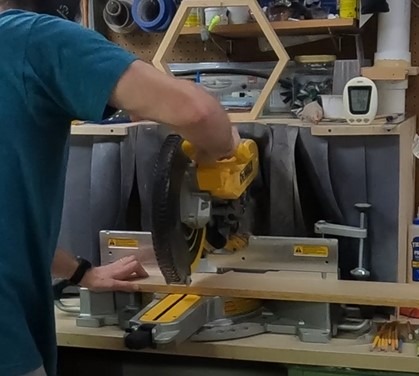
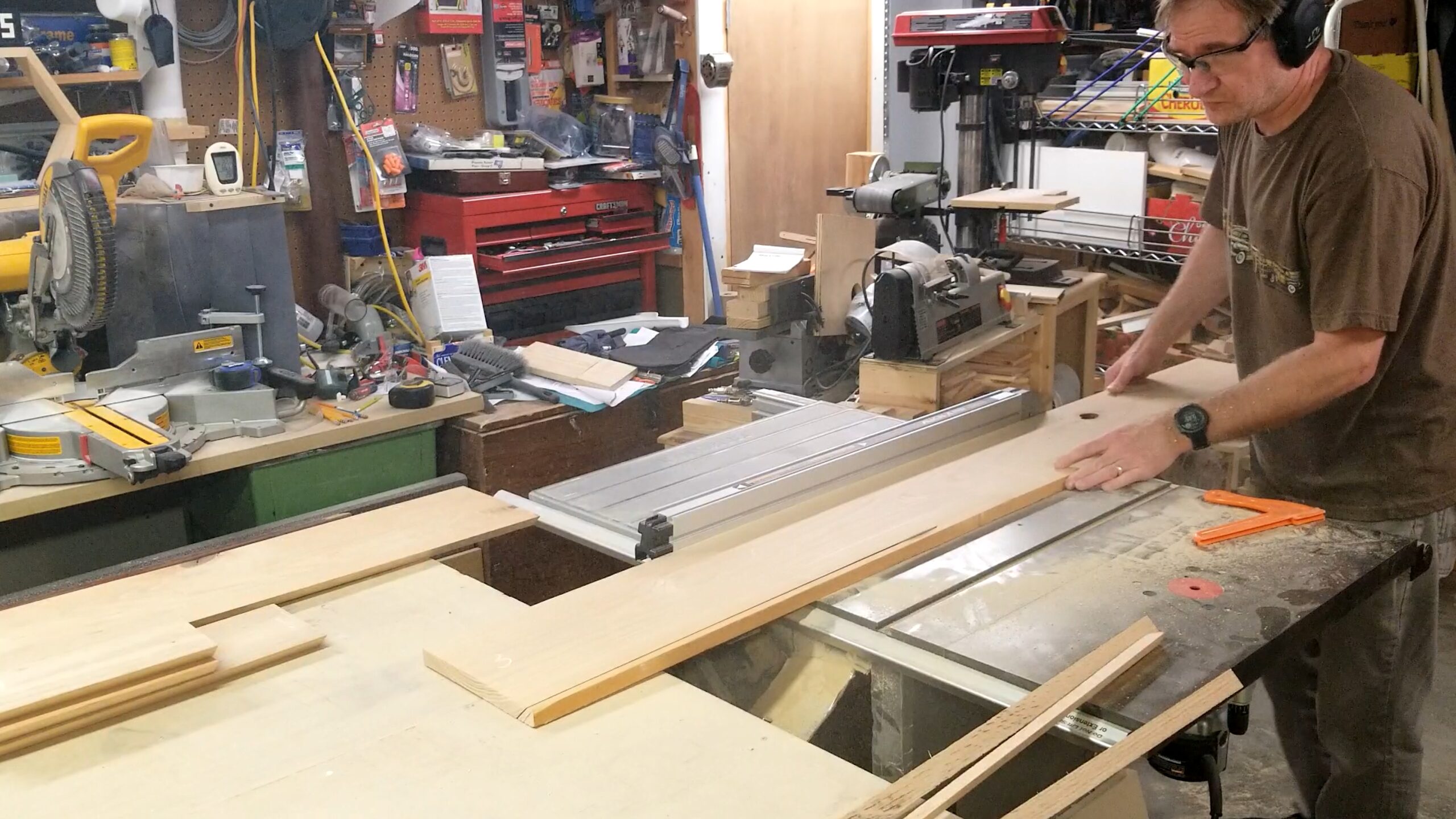
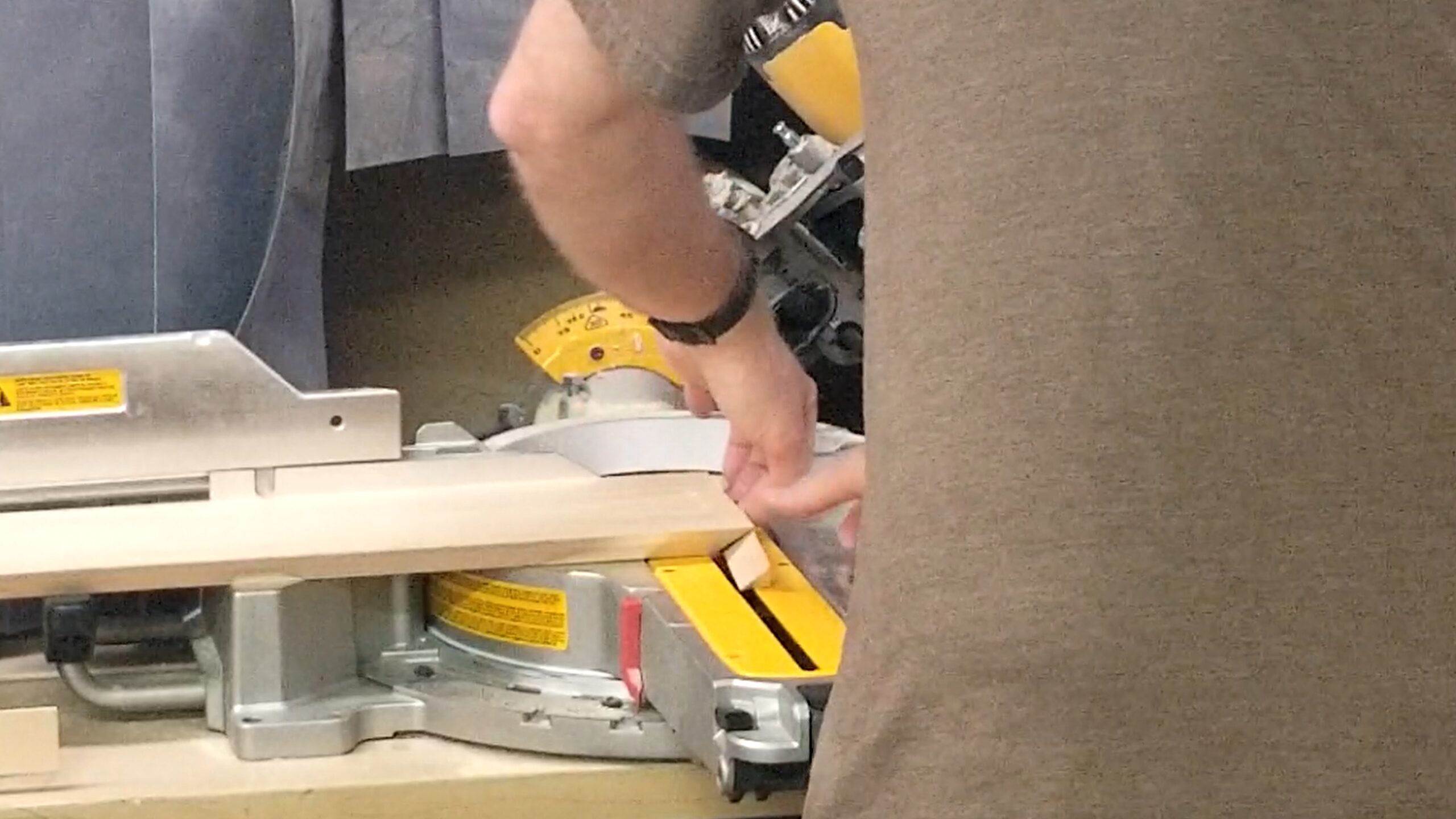
Once everything is cut to the proper sizes I start by taping up any places I have knots or cracks. I’m going to fill the cracks with clear epoxy and the knot whole with dyed epoxy. I needed to create two layers of epoxy because not all the bubbles came out after I poured it and after it had been sanded smooth, there were open bubbles so I had to refill them and sand again. No biggie. I used JB Weld 2-part epoxy, which was probably not the best kind, but it was cheaper and I only needed a couple of ounces.
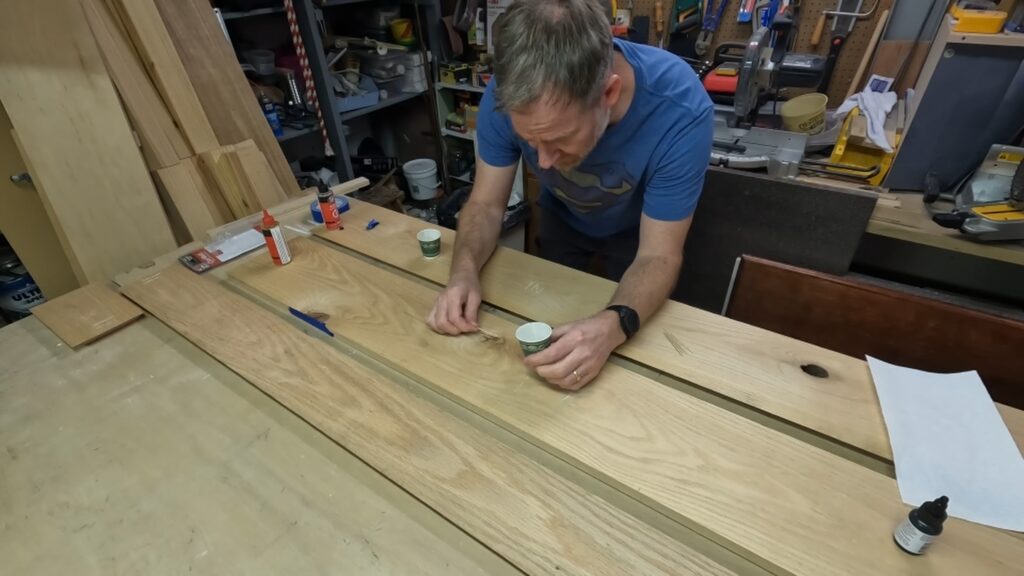
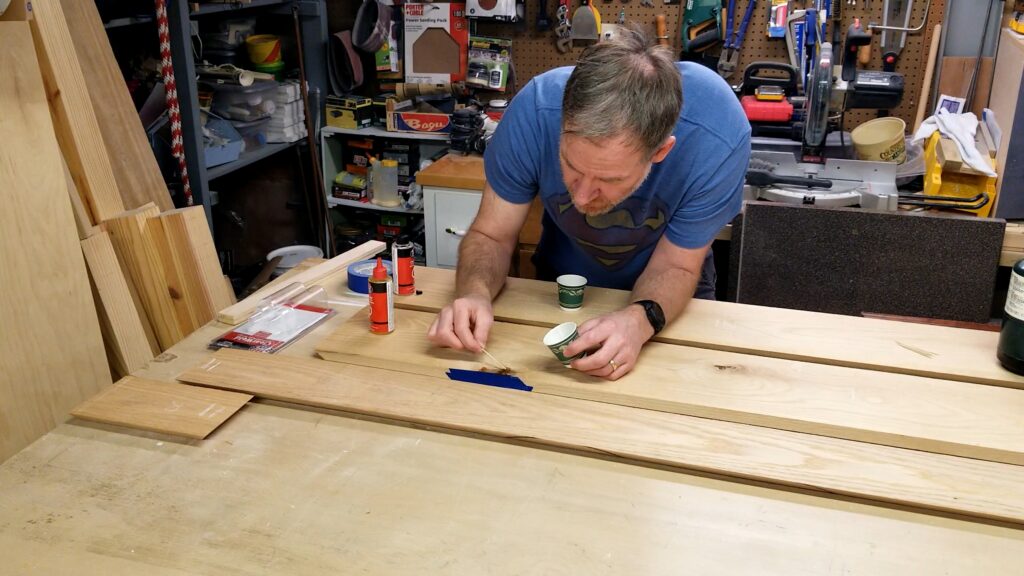
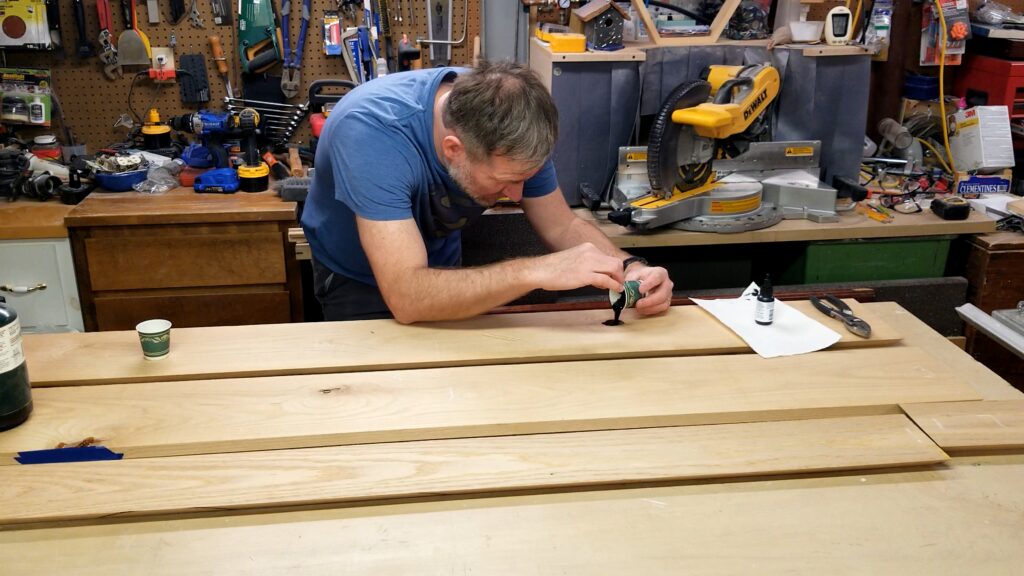
Once the epoxy had thoroughly cured and been sanded smooth, I continued by gluing the miters using painter’s tape to roll the pieces together. I use a few 23 gauge pin nails with my pin nailer trying to hit the grain to hide the pins. These are only there to hold the pieces of wood together until the glue sets up.
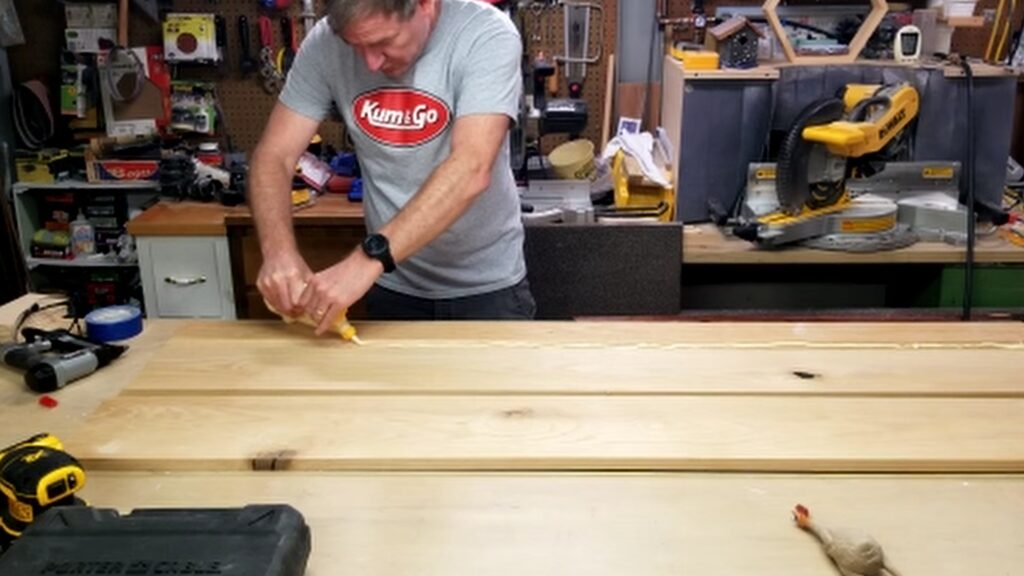
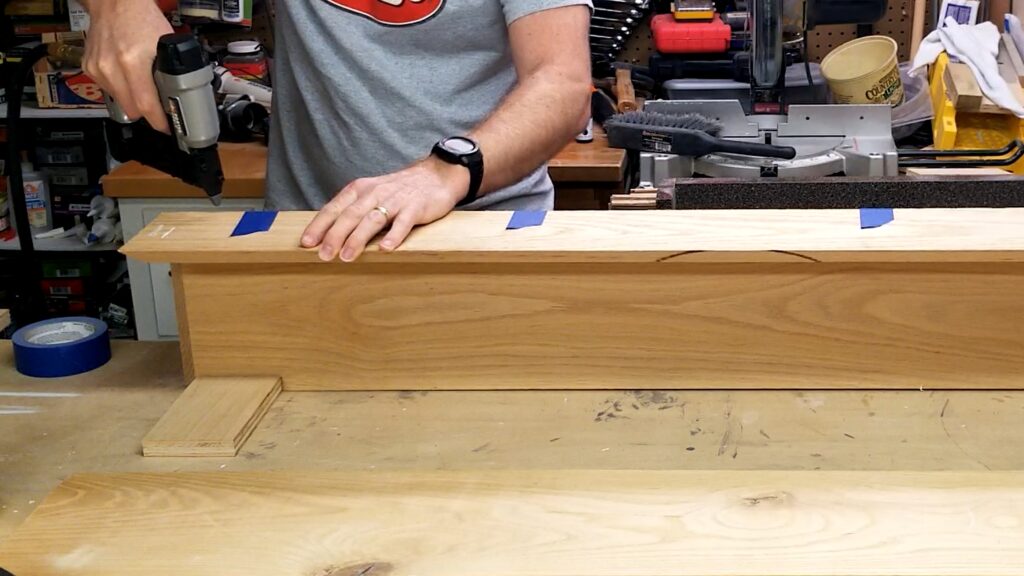
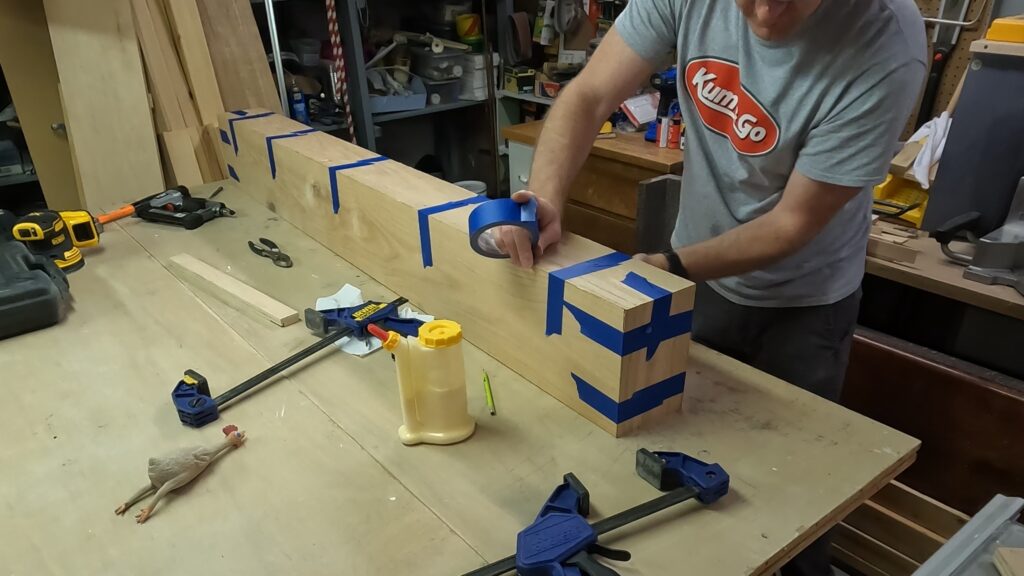
Continuing I cut the ends to the right lengths and glue and pin these into the ends. I thoroughly taped all the joints up with painter’s tape so everything is nice and tight since using clamps on this thing would be more difficult.
After the glue sets up I do have some joints that were a little loose but that’s okay. I mixed up some glue and sawdust and smashed it into the cracks. I’ll sand these down and it will just look like one good beam.
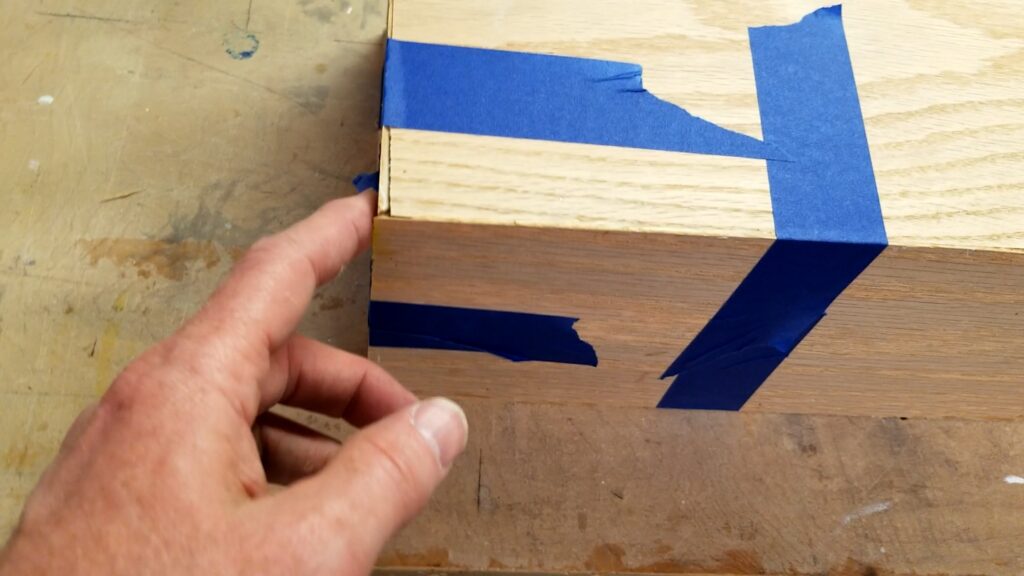
I thoroughly sand and repeat the crack-filling process until everything is exactly how I want it. Is it perfect? No, and I don’t want perfect. I want it to be a little rustic but not completely beat up.

I constructed a 2 x 4 blind shelf support that I can bolt to the fireplace and the mantel will just slide onto. I can secure the mantel from above, underneath, or wherever I want.
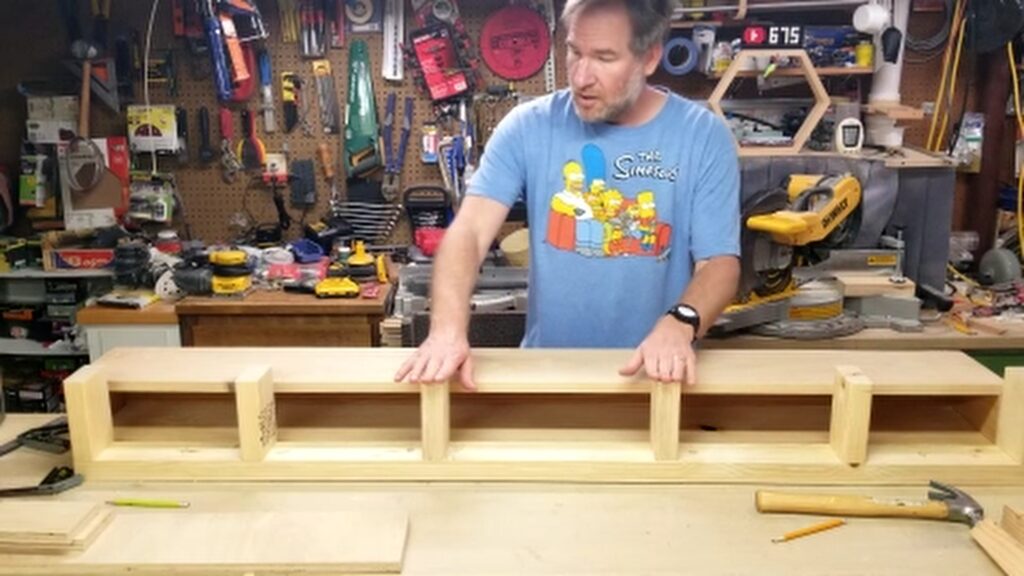
After working my way up from 80 grit to 220 grit sandpaper I prepare the mantel for staining and a polyurethane top coat. I use Minwax Slate Wood Finish for the stain and once that has cured I apply 3 coats of Varathane Satin Polyurethane.
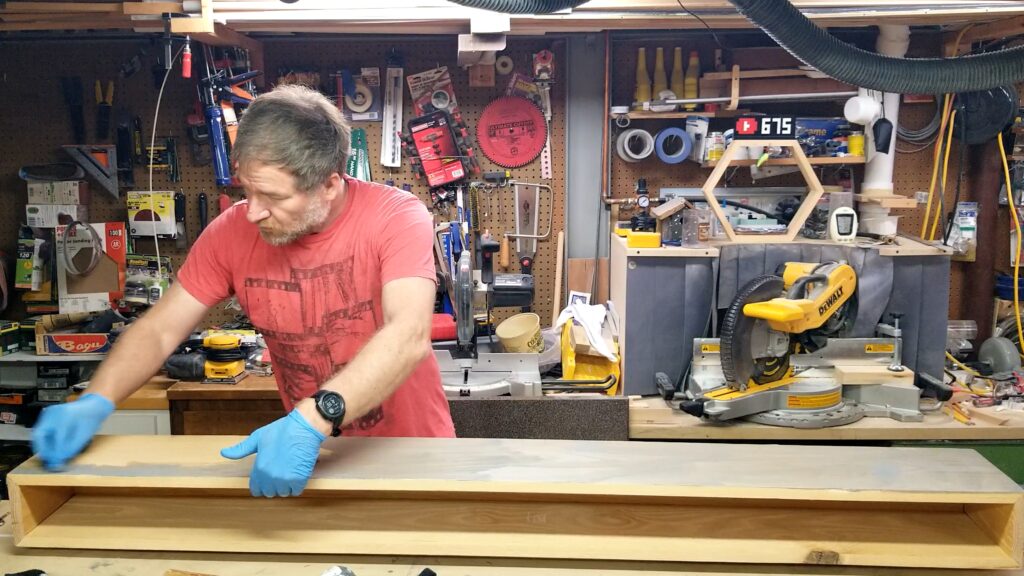
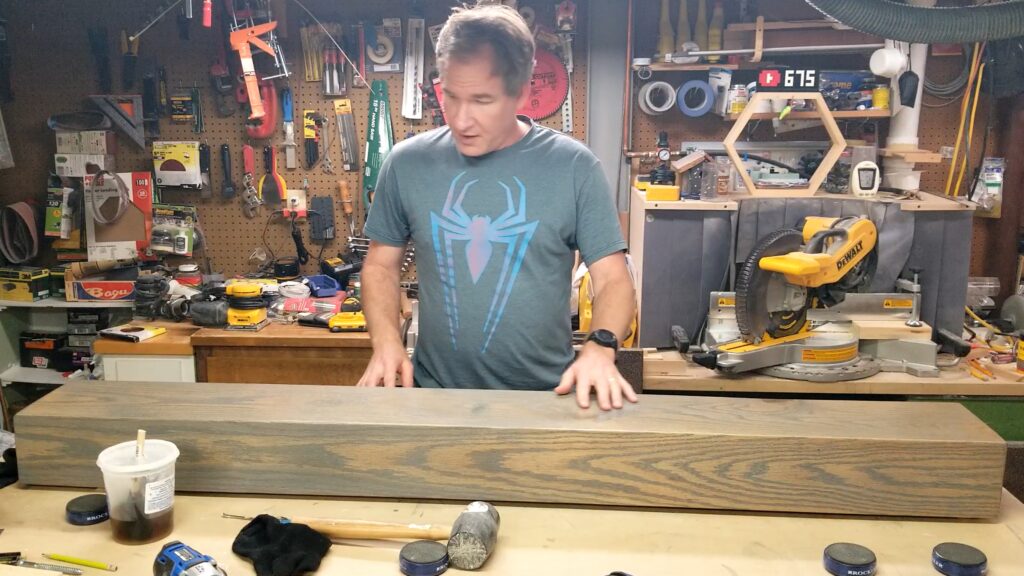
To mount the mantel on my stone fireplace I do have to do a little wood carving with a wood rasp to get the stone contours. Once that is done it slides right onto the support and fits tight up against the stone.
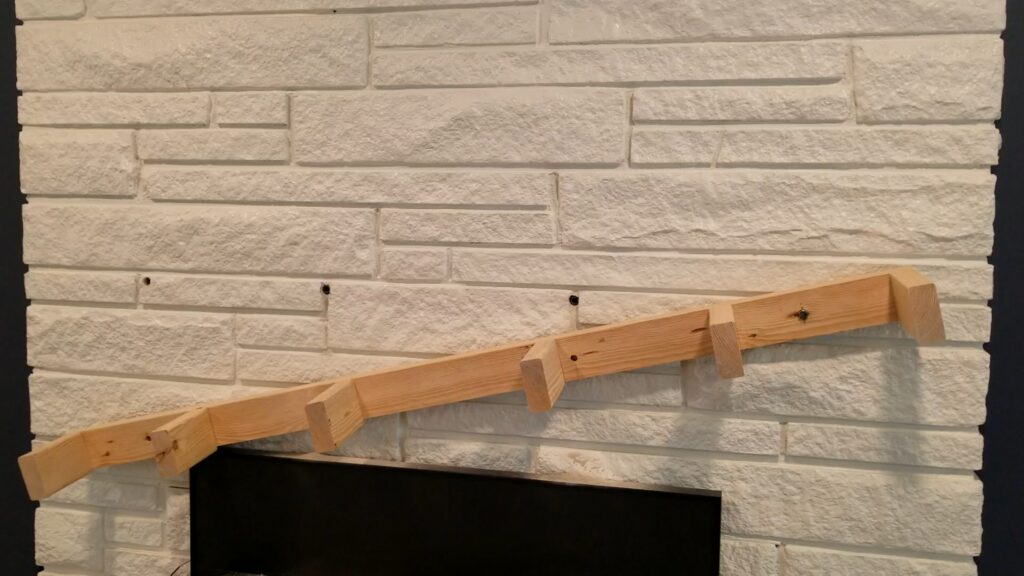
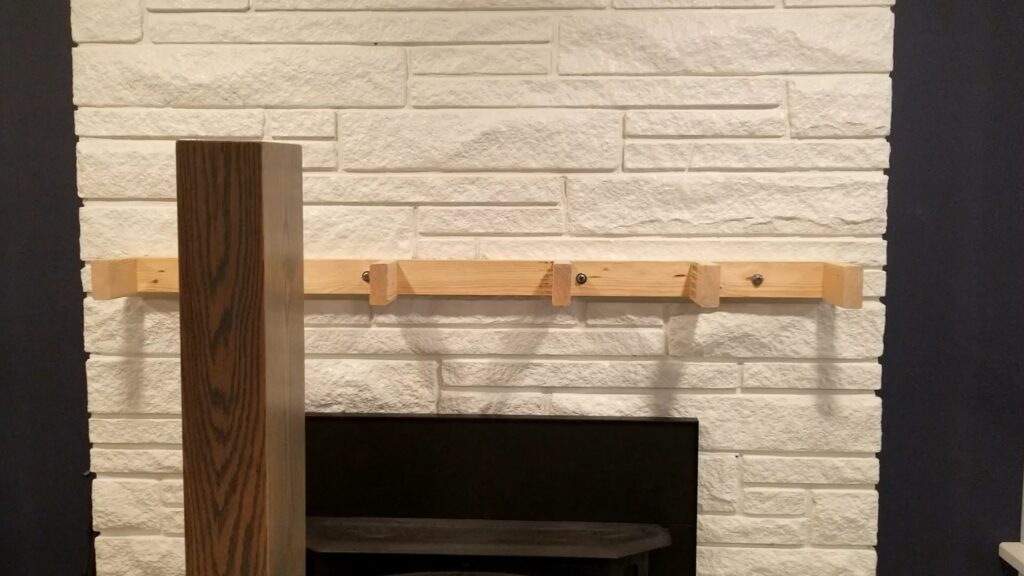
I believe this project turned out great and looks nice. What do you think?
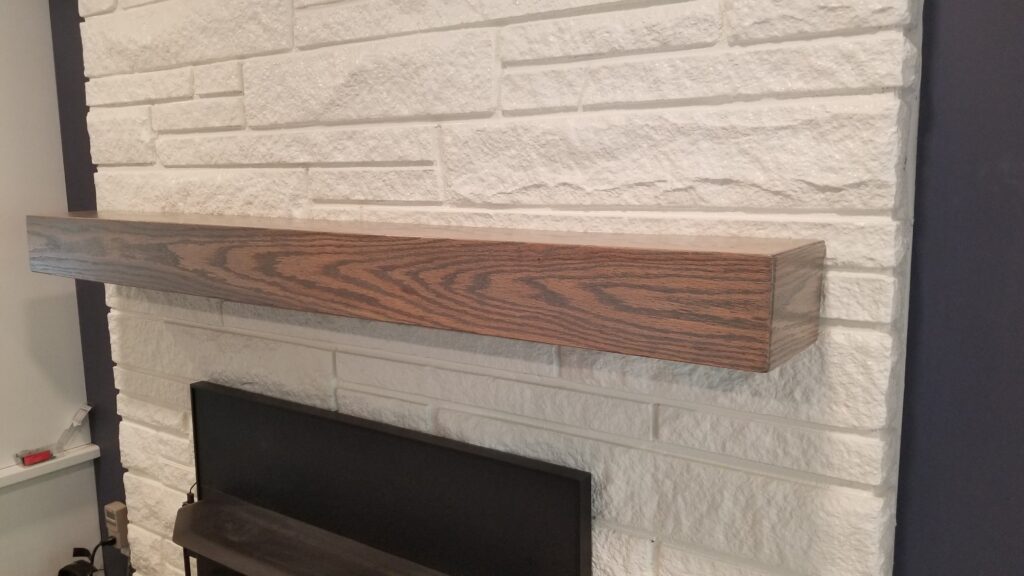
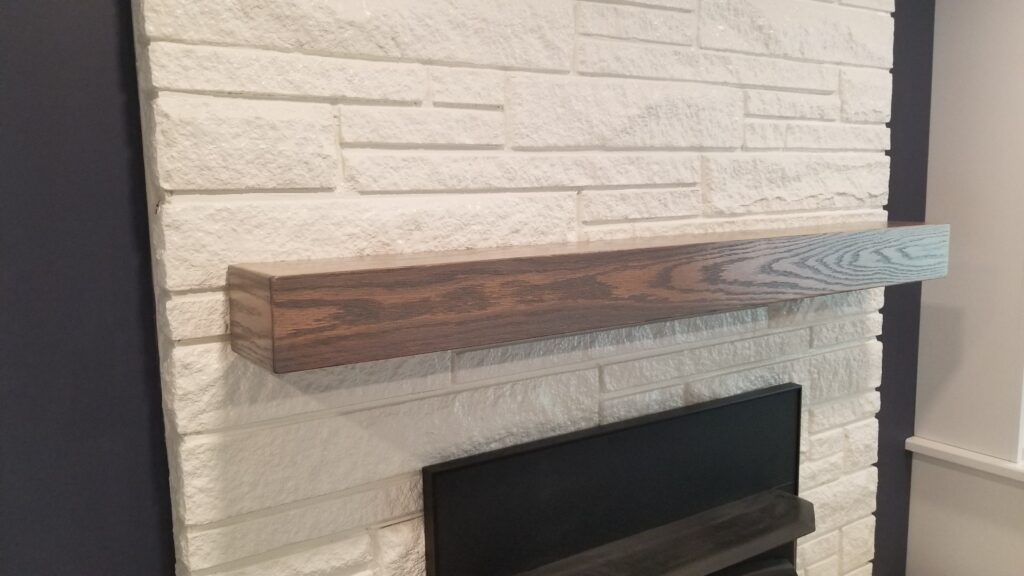
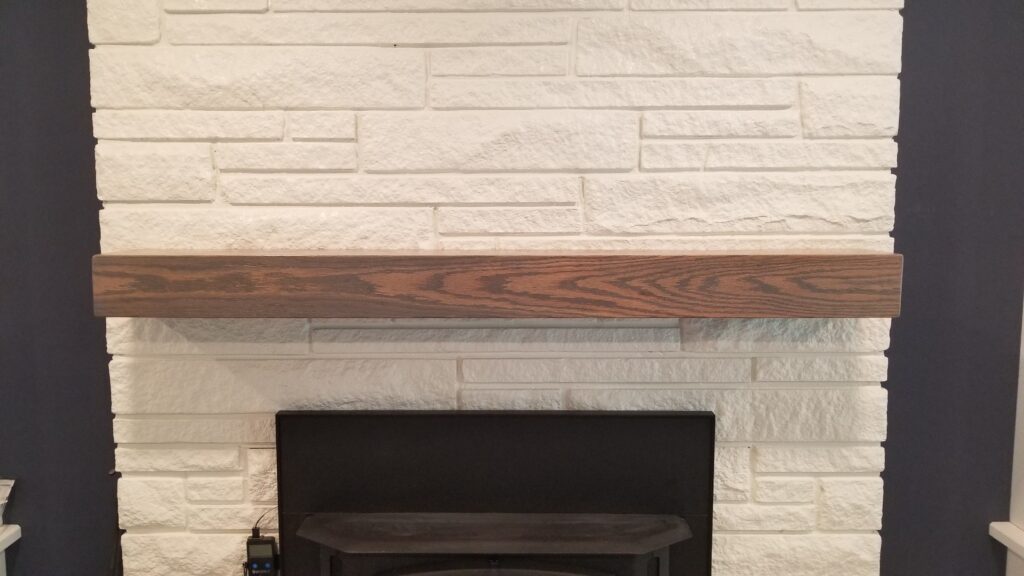
Head on over to YouTube by clicking on the video below and see how it was made and turned out.
Equipment and Materials
I hope you find this helpful video useful and can use some of the tips presented. Feel free to leave any comments, suggestions, or experiences you have had below.
Some of the links in my video description and article above are Amazon Affiliate links. As an Amazon Associate, I earn from qualifying purchases. If you would like to make a different purchase from Amazon, you can also use the storewide link.
Play-Doh Modeling Compound 10-Pack Case of Assorted Colors, Non-Toxic 2 oz. Cans, Back to School Gifts & Prizes for Students & Classroom, Preschool Toys for Kids, Ages 2+ (Amazon Exclusive)
36% Off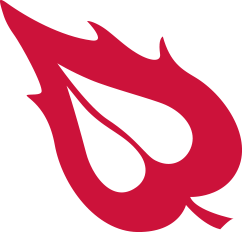